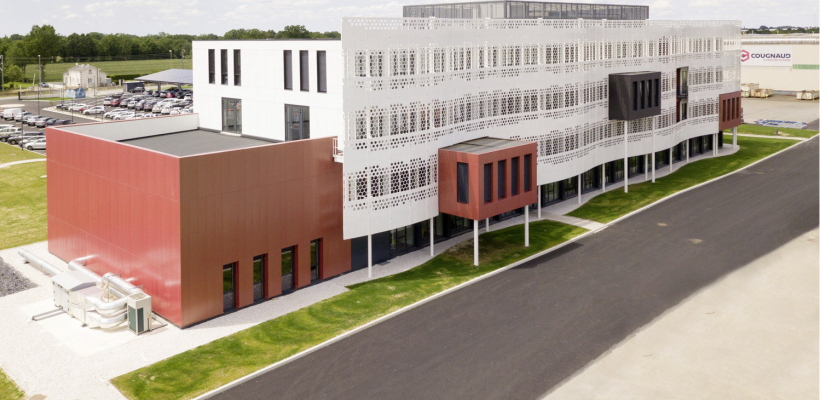
À Mouilleron-le-Captif (85), le bâtiment modulaire "Cougnaud Campus" accueille les équipes de Cougnaud Construction depuis l'année dernière. D’une superficie de 5 000 m² (R+3), il se veut particulièrement exemplaire notamment en produisant plus d'énergie qu'il n'en consomme. Pour assurer l'étanchéité de sa toiture, une phase de prototypage menée durant plusieurs mois, a validé la mise en œuvre d'une membrane EPDM (Rubbergard de Firestone) fixée sur des panneaux bois CTBH ou OSB.
Sur le terrain, la membrane a été intégrée au process modulaire après nettoyage du support, dépliage du rouleau, coupe des longueurs, encollage puis finition des rives périphériques et des entrées d’eaux pluviales en bas de pente. Disponibles dans plusieurs largeurs, les nappes ont permis une étanchéité totale, sans aucun joint. Les raccords d'étanchéité entre chaque élément ont été réalisés par bandes de pontage.
Suite à cette première opération, la collaboration entre les deux partenaires se poursuit avec une installation des membranes directement sur les modules en usine. Le procédé est sous ATEx.